At Haydon Companies, no phase of operation or administration is of greater importance than safety and accident prevention. In all of its operations, Haydon is guided by an established accident-prevention plan which is based upon our sincere desire to eliminate occupational injuries and illnesses, eliminate damage to equipment and property, and protect the general public. Although we pride ourselves on our outstanding production rates, safety is never sacrificed for production. Our commitment to safety is reflected in our extremely low Incident Rate (IR) and Experience Modification Rate (E-MOD).
“Haydon Companies will establish and maintain – throughout the entire organization – the firm belief that people are our most important assets, and protecting our employees has management’s highest priority, support, and participation.”
- Katie Haydon, President & CEO
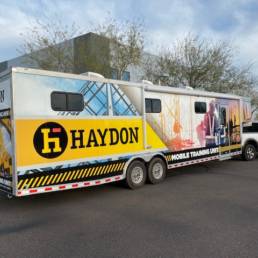
Leading the way for Haydon's Safety Vision
Haydon's Mobile Training Unit
Haydon kicked off its Mobile Training Unit in early 2019 to help SHARE INFORMATION and MAKE SAFETY A PRIORITY. This shows the determination to continually educate Haydon employees and empower them with knowledge. Our mobile classroom provides engaging and interactive instruction onsite at any project location. Training is conducted around the crews’ schedules. By coming directly to the project site, our mobile training unit is increasing the accessibility for crews to receive training, which is a vital part of keeping crews safe during daily operations.
What Does Safety Mean to Me?
We Are Transparent With Our Safety Culture
Early 2020, Haydon launched the weekly Safety Toolbox Talk email in order to encourage Sharing Information and Embracing Improvement. Our Toolbox Talk email fosters our safety culture by sharing company-wide safety statistics and training opportunities. Each week is a different topic which is then discussed at the beginning of the week with all of our teams in the field. Awareness of potential safety issues through resources like our Safety Toolbox Talk is key to preventing further issues and assures that our teams go home to their families safely on a daily basis.
Haydon’s award-winning safety program is led by our safety team, whose sole responsibility is to ensure that, at every level of our organization, we are maintaining our unwavering commitment to safety.